SICE Industry
Special Talk
Implementing semantic interoperability
Dr.-Ing. Thomas Hadlich
Chairman of IEC TC65/WG16 "Digital Factory"
Global Product Standards and Regulations, Rockwell Automation, Germany
Date and Time: Sept. 7th, 9:20-10:20
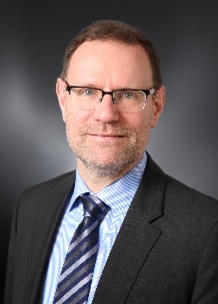
AbstractIn order to meet customer needs and requirements enterprises today form value creation networks among multiple enterprises and across multiple nations. Tight cooperation only succeeds if the involved enterprises share information. Such information may describe customer requirements, working processes or the delivered good (like intermediate products and components). Cost reduction and optimization in such international value adding networks can be achieved only if semantic interoperability is achieved. Interoperability among various enterprises and across nations can be based only on international standards. The Digital Factory Framework (DFF) (IEC 62832) provides a fundamental concept for sharing information among enterprises. It describes an approach that covers the life cycle of a production system from basic engineering to decommissioning. While the standard provides fundamental concepts and definitions, the actual implementation needs to be based on standards which define data exchange formats like BMEcat, Asset Administration Shell (IEC 63278), Automation ML (IEC 62714), FDT (IEC 62453), FDI (IEC 2769) and OPC UA (IEC 62541). The information shared across a value creation network basically has 2 directions: Product requirement information is transmitted from customer to supplier of the final product and accordingly to the providers of product materials and components. Product description information flows from providers of product materials and components towards the supplier of the final product and to the end customer. Such product description information includes information about the delivered goods and may as well contain data from the production process (e.g., production conditions that influence product quality). Quality data of intermediate products may be used to optimize the following production steps and to meet the overall quality requirements of the product. An equipment supplier will have to be able to support the supply chain (when the equipment is the product) as well as to support exchange of information from the use of the equipment (when the equipment is used to produce another product). This contribution focuses on the flow of information towards the end customer and explores how semantic interoperability can be implemented and what it means for an equipment supplier. It is discussed which fundamental common requirements defined by the DFF apply to the different data models, how different data formats are used in the system life cycle and how semantic interoperability can be achieved between the different data models.
BiographyThomas Hadlich studied Electrical and Automation Engineering at Otto-von-Guericke University Magdeburg, Germany. After graduation as Diploma-Engineer he worked as manager for software development at ifak system GmbH. After 12 years of developing device integration solutions based on OPC, FDT and EDD, Thomas went in 2010 back to University Magdeburg, worked as a researcher at the Institute for Automation Engineering, and graduated with Dr.-Ing. in 2015. Since 2017 he is working at Rockwell Automation. Thomas Hadlich has been working since the 1990s in standardization groups focused on device integration, for instance DRIVECOM User Group, OPC Foundation and Profibus User Group. Since 2005 he is participating in international standardization at IEC. Today Thomas Hadlich is chairman of IEC TC65/WG16 “Digital Factory”, editor of SC65E/WG4 “FDT”, leads the project “Digital Nameplate” at SC65E/WG2 and is member in other working groups like TC65/WG24 “AAS” and in SC3D “Classes, Properties and Identification of products - Common Data Dictionary (CDD)”. Also, he is chairman of working groups at FDT Group and of the FDT joint working group at OPC Foundation.